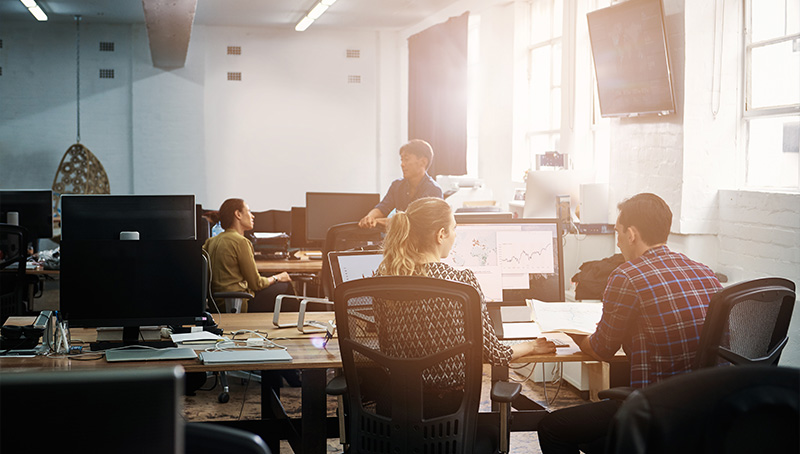
Mehr Produktivität in der Umschlaghalle
Nutzen Sie das ganze Potenzial Ihrer Umschlaghalle
Jede Umschlaghalle hat ihre Besonderheiten. Ihre Produktivität mit einem speditionsweiten Benchmarking zu messen, hieße Äpfel mit Birnen zu vergleichen. Klarheit schafft nur die genaue Kenntnis der Prozesse. Hier tickt jede Halle anders. Layout, Güterstruktur, Personaleinsatz und äußere Bedingungen wirken höchst unterschiedlich auf ihr Leistungsvermögen ein. Daher arbeiten wir immer erst die Prozess-Spezifika heraus, bevor wir das Optimierungspotenzial einer Halle ermitteln und gemeinsam mit unseren Kunden umsetzen.
Inhalte
Im Zentrum der Analyse stehen die Hallenabläufe. Passen die Ein- und Ausgangsprozesse zu Layout, Stellplatzkonzept, Güterstruktur und Personaleinsatz Ihrer Halle? Unsere IST-Aufnahme deckt präzise auf, wie gut die unterschiedlichen Faktoren aufeinander abgestimmt sind.
Um die Stärken und Schwächen präzise aufzudecken, achten wir auf alle Prozessdetails. Werden Stapler oder Schnellläufer eingesetzt? Wie ist das Verhältnis Colli je Bewegung in den Entlade- oder Verteilprozessen? Welche Wege legen die Verlader zurück? Und viele Fragen mehr.
Mögliche Antworten gibt es viele. Um die lohnendsten aufzuzeigen, modellieren wir Alternativprozesse und errechnen die sich daraus ergebenden Produktivitätszuwächse. Belastbar zeigen wir z.B. auf, wie stark ein neues Stellplatzkonzept die bisherige Verladerauslastung steigert.
Umschlaghallen erreichen ihr Produktivitätsmaximum, wenn alle Abläufe optimal aufeinander abgestimmt sind. Daher achten wir bei jeder Maßnahme immer auch auf das Gesamtbild: Zusätzlich zum Teilprozess behalten wir die Wirkungen auf alle anderen Bereiche im Blick.
Wir begleiten Sie bei der Umsetzung unserer Konzepte. Dies gilt auch für die Zeit danach. Hierzu erhalten sie ein Set an Produktivitätskennzahlen, das individuell auf Ihre Halle und deren Abläufe abgestimmt ist. Mit diesem Controlling messen Sie den Erfolg der Reorganisation.
Use Cases
„Ist meine Unterflurförderkette noch wirtschaftlich?“ Mit dieser Frage kam eine Stückgut-Kooperation auf uns zu, die eine gut 7.000 m2 große Umschlaghalle automatisiert hatte. Seit 20 Jahren stützte sich die Colli-Verteilung auf eine Unterflurförderkette – sowohl im Ein- als auch Ausgang.
Wirtschaftlichkeitsanalyse
Eine kaufmännisch sinnvolle Entscheidung? Um dem Kunden belastbare Antworten zu liefern, machten wir uns ein genaues Bild vom Hallenlayout, der Prozessorganisation und der Integration der Kette. Die Ist-Aufnahme zeigte: Der Einsatz der Kette und das damit verbundene Handling verlangsamten ausnahmslos alle Umschlagprozesse.
Erfolgreiche Reorganisation
Um unseren Kunden mit dieser Bestandsaufnahme nicht allein zu lassen, haben wir ein alternatives Hallenkonzept ausgearbeitet. Der Umstieg auf Schnellläufer und Stapler sowie die Einführung fest definierter Entladezonen nahmen darin Schlüsselrollen ein. Die Produktivitätszuwächse summierten sich auf bis zu 25 % mehr Colli pro Mitarbeiterstunde. Genug, damit uns der Stückgut-Dienstleister den Auftrag gab, das neue Konzept umzusetzen. Bereits sechs Monate später hatte die Halle die prognostizierten Effekte erreicht.
Vorgehen und Nutzen in der Detailsicht
Unterflurförderketten – Anspruch und Wirklichkeit
Unterflurförderketten eignen sich für Umschlaghallen, in denen ausreichend viele Colli über große Distanzen zu transportieren sind. Soviel zur Theorie. Doch ab welcher Weglänge zahlt sich die Automatisierung auch in der Praxis aus? Wie präzise sollte eine Halle den Einsatzbereich ihrer Kette ausrichten? Unter Umständen nur auf den Sammelgutausgang, wenn auch die NV-Fahrer in den Prozess mit eingebunden sind? Und führt das Hubwagenhandling wirklich zu geringeren Arbeitsaufwänden als die Verteilung mit Staplern oder Schnellläufern? Auch dann, wenn man das Ein- und Ausschleusen der Colli mit auf die Rechnung nimmt? Antworten auf diese Fragen liefert eine detaillierte Aufnahme der physischen Gegebenheiten und gewerblichen Abläufe in der Halle. Um die Wirtschaftlichkeit der Kette präzise aufzuzeigen, stehen drei Themen im Fokus:
- Einbindung der Kette in das Hallenlayout
- Verteilprozesse inkl. Hubwagenhandling
- Auswirkungen auf andere Prozesse
Kettenorganisation – mangelnde Koordination der einzelnen Verteilprozesse
Zurück zum Kundenbeispiel der Stückgut-Kooperation. Um die Performance der Kette vollständig zu messen, waren wir sieben Tage lang rund um die Uhr in der Umschlaghalle. Die Vor-Ort-Aufnahme machte sowohl layout-bezogene als auch organisatorische Mängel sichtbar. Aus Layout-Sicht fiel auf, dass die Kette weder richtig innen- noch außenliegend war. In der Konsequenz wurden die Relationsplätze durch die Kettenspur getrennt, was häufige Wege „durch die Kette“ zur Folge hatte. Zudem deckte die Unterflurförderkette nicht die gesamte Hallen-fläche ab, so dass zusätzliche ungeplante Verteilprozesse erforderlich wurden.
Hohe Suchkosten
Erhebliche Zusatzaufwände traten auch beim Handling der leeren Hubwagen auf. Vor allem zu Spitzenzeiten standen den Mitarbeitern an den Schleuspositionen nicht ausreichend viele leere Hubwagen zur Verfügung. Dies galt sowohl für das Einschleusen der Colli in die Kette als auch für den Rücktransport von Paletten an den Ausschleus-Positionen. Um drohende Blockaden zu vermeiden beziehungsweise bereits entstandene Engpässe aufzulösen, suchten die Hallen-mitarbeiter regelmäßig auf eigene Faust nach beladbaren Hubwagen.
Kettenbezogenes Handling
Zusätzlich zu den ungeplanten Zusatzaufwänden zeigte unsere Analyse aber auch die Prozesszeiten auf, die der Betrieb der Kette erforderlich machte. Vor allem der Blick auf die Wartezeiten an den Ausschleuspositionen führte zu einem echten Aha-Erlebnis bei unserem Kunden: Insbesondere in den Nebenzeiten fielen dort so ausgedehnte Wartezeiten an, dass die Produktivität der Kette im Vergleich zu einer rein manuellen Verteilung deutlich ins Hintertreffen geriet.
IST-Ergebnis
Da die Einzelschritte des Verteilprozesses nicht ausreichend koordiniert waren, blieb die Geschwindigkeit des automatisierten Transports unter ihren Möglichkeiten. Die mangelhafte Integration der Kette in das Hallenlayout tat ein Übriges. Im Endergebnis bremsten der Einsatz der Kette und das damit verbundene Handling sämtliche Umschlagprozesse deutlich aus. Spiegelbildlich zu den längeren Prozesszeiten erhöhten sich auch die Prozesszeiten der Colli: Im Schnitt überschritt die untersuchte Halle unsere Benchmark-Zeiten um 68% .
Lösung
Vor dem Hintergrund dieser Wirtschaftlichkeitsanalyse haben wir ein neues Hallenkonzept ausgearbeitet und Anfang 2014 erfolgreich umgesetzt. Kern des Konzepts war die vollständige Ablösung der Kette durch manuelle Verteilprozesse mit Schnellläufern und Staplern. Zweifellos ein tiefer Einschnitt für eine Halle, die rund zwanzig Jahre lang auf eine Unterflurförderkette gesetzt hatte. Um ausreichend Rückendeckung für das neue Konzept zu bekommen, haben wir zusätzlich zu den Verantwortlichen in der Halle auch das leitende Management von der Machbarkeit unseres Ansatzes überzeugt.
Durchgängiges Handling
Das neue Betriebskonzept umfasst alle Hallenabläufe bis zur Verladung, die in Teilen ebenfalls neu ausgestaltet wurde. Gleichwohl lag der Schwerpunkt der Anpassungen auf den Entlade- und Verteilprozessen. Die sichtbarsten Veränderungen waren der Wechsel zu fest definierten Entladezonen und die Umstellung der Verteilung auf ein rein manuelles Handling mit Staplern und Schnellläufern.
Erfolg nach wenigen Monaten
Bereits sechs Monate nach der Umstellung erreichte die Halle die Sollzeiten, die wir zuvor mit unseren Benchmark-Daten errechnet hatten. Aus Sicht der Stückgut-Kooperation bedeutet dieser Leistungszuwachs, dass die Halle in Spitzenzeiten jetzt bis zu 25% mehr Colli pro Mitarbeiterstunde umschlagen kann. Übrigens ganz ohne einen Anstieg der Schadensquote. Angesichts der erreichten Mehrwerte arbeitet die Halle auch heute noch – beinahe zwei Jahre nach ihrer Umstellung – mit dem manuellen Betriebskonzept. Und dies mit anhaltendem Erfolg.